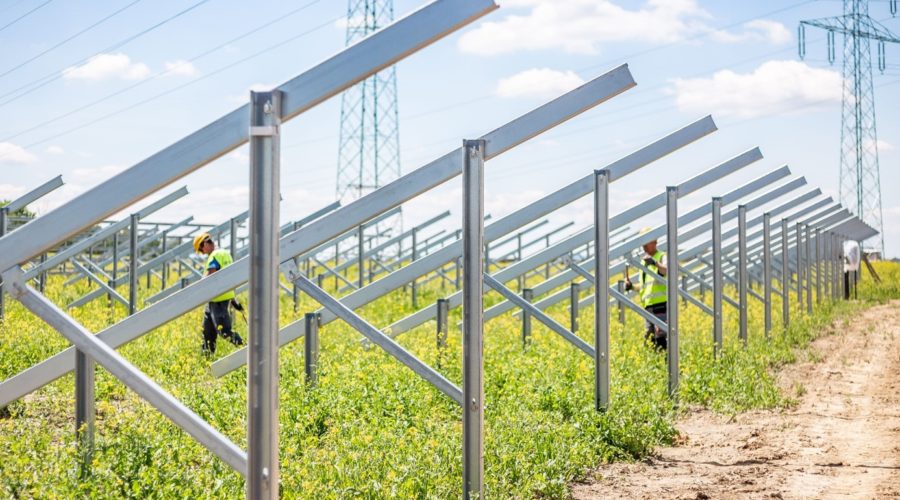
Energy5 – the precursor of structural research in the field of corrosivity
Photovoltaic structures are directly exposed to weather conditions – therefore they must be resistant to wind and snow loads and, importantly, they must meet the relevant corrosion resistance standards.
The aim of the article is to introduce the participants of photovoltaic investments to the subject related to the requirements that should be met by ground substructures in terms of corrosion durability.
This issue is very often underestimated when designing the installation or the implementation itself. It often happens that manufacturers of substructures, without their own research for entire sets of products (prefabricated structure, connectors, PV panels), use the marketing materials of suppliers of semi-finished products that are used for the production of photovoltaic structures.
To ensure the long-term corrosion durability of the photovoltaic system, it is important to use the charge material – high-strength steel, however, other aspects are also very important, such as:
- an appropriate prefabrication process of the batch material that will meet the assumptions of the manufacturer of sheet metal with an anti-corrosion coating,
- contact of other materials cooperating with each other on a daily basis in the used installation (e.g. according to the guidelines of the manufacturer of the charge material, such materials as stainless steel elements must not come into contact with the coating in corrosion class C4 and C5),
- contact, for example, with a concrete mix in places where piling does not provide adequate parameters for the foundation of the structure,
- contact with aluminum elements of PV module frames.
A manufacturer of photovoltaic structures without performing the above tests in accredited laboratories has no grounds to provide a guarantee for the corrosion resistance of the product set. In connection with the above, the investor of a photovoltaic installation, who is faced with the choice of mounts for PV modules, should ask the manufacturer to present the above-mentioned tests. This approach will allow you to verify on what basis the manufacturer actually provides a warranty for corrosion resistance and whether appropriate tests have been carried out.
Corrosive categories of the environment
Structures for photovoltaic modules should meet the requirements for the corrosive category of the environment, min. C3 – urban and industrial environments characterized by medium pollution with sulfur oxide (IV), coastal areas with low salinity, C4 – industrial areas and coastal areas with moderate salinity, or C5-I – industrial areas with high humidity and aggressive atmosphere.
According to the PN-EN ISO 12944-2: 2001 standard, we distinguish the following atmospheric corrosivity categories and examples of typical environments:
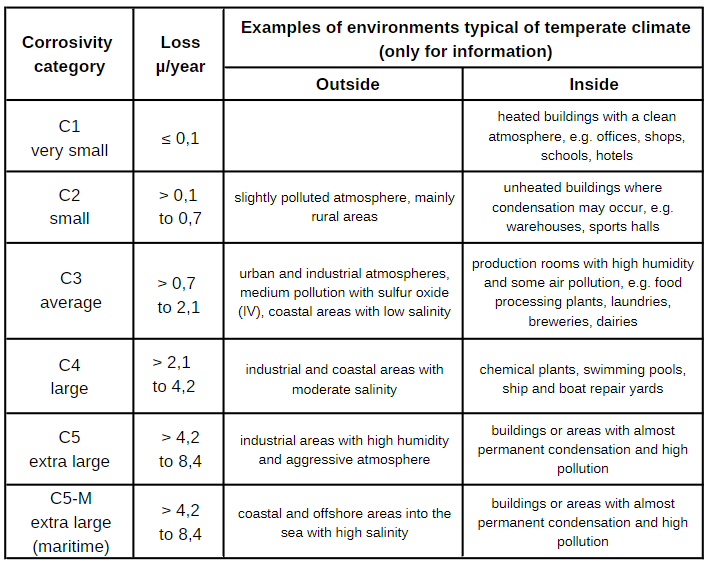
Currently on the market, technical specifications usually require that the substructure as a set has tests confirming that it is dedicated to the corrosive category of the C5 environment. It should be emphasized that it is the whole set, and not the tests of the batch material intended for making the load-bearing elements. It is also worth noting that the general guidelines of the steel manufacturer do not allow this material to be used in a highly aggressive environment or allow it, but with many limitations.
Energy5 Sp. z o.o. places great emphasis on providing only durable and safe fasteners and is one of the few companies on the market to test its structures in laboratories accredited for corrosion resistance. As a result, the company has a much wider range of options for configuring the substructure as a set of products than it results from the general guidelines of the manufacturer of the input material.
The scope of corrosion tests of Energy5 structures includes:
- elements of the prefabricated structure (legs / purlins / rafters) subjected to the effects of neutral salt spray according to PN-EN ISO 9227: 2017-06 in the scope of continuous spraying 1440 h, which corresponds to corrosion class C5,
- elements of the prefabricated structure (legs / purlins / rafters) subjected to the effects of neutral salt spray according to PN-EN ISO 9227: 2017-06 in the range of 2000 h continuous spraying and cyclic sampling with sulfur solution. The tests confirmed the possibility of using the Energy5 products on heaps after mining sulfur mines,
- structure elements drilled at the construction site or mechanically cut, subjected to the effects of neutral salt mist according to PN-EN ISO 9227: 2017-06 in the scope of continuous spraying 1440 h, which corresponds to corrosion class C5,
- structure elements with screwed bolts and stainless washers, subjected to the effects of neutral salt spray according to PN-EN ISO 9227: 2017-06 in the scope of continuous spraying 1440 h, which corresponds to corrosion class C5,
- structure elements with screwed bolts and galvanized washers, subjected to the effects of neutral salt spray according to PN-EN ISO 9227: 2017-06 in the range of continuous spraying 1440 h, which corresponds to corrosion class C5.
- construction elements with stainless steel frames bolted through screws, subjected to the effects of neutral salt spray according to PN-EN ISO 9227: 2017-06 in the range of continuous spraying 1440 h, which corresponds to corrosion class C5,
- elements of the structure cut on a laser, subjected to the effects of neutral salt mist according to PN-EN ISO 9227: 2017-06 in the range of continuous spraying 1440 h, which corresponds to the corrosion class C5,
- elements of the structure protected with zinc paint after the tiling process, subjected to the effects of neutral salt mist according to PN-EN ISO 9227: 2017-06 in the scope of continuous spraying 1440 h, which corresponds to the corrosion class C5,
- structure elements concreted as single elements and two U-profiles with their backs, subjected to neutral salt spray according to PN-EN ISO 9227: 2017-06 in the scope of continuous spraying 1440 h, which corresponds to corrosion class C5,
- comparative analysis of various sheet metal forming processes in the context of the evaluation of the quality of the protective coating.
The corrosion damage of the above tests was assessed according to PN-EN ISO 10289: 2002.
The tests confirmed that the substrate corrosion parameters (rust) of RP 10 were met and showed that the technology of the Energy5 Sp. z o.o. meets the highest standards of corrosion protection. Thus, all structural elements, regardless of their thickness, achieved the highest corrosion protection parameters required by the standards.
Energy5 Sp. z o.o. is a precursor of research into photovoltaic structures – especially in terms of their corrosivity. The company has relevant data, and these allow it to select the appropriate photovoltaic structures that take into account the corrosive categories of the environment and soil conditions. This approach assures investors and contractors of photovoltaic investments that the manufacturer’s guarantees are granted only on the basis of tests of entire sets of products and are justified. It is worth recalling that the company was the first and the only one on the market to obtain the National Technical Assessment, which is an undeniable confirmation of the most advanced solutions, going beyond the solutions used on the market under the harmonized standard PN-EN 1090-1.

Photo no. 1. Elements of the Energy5 structure concreted. Exposure time 1440 h.
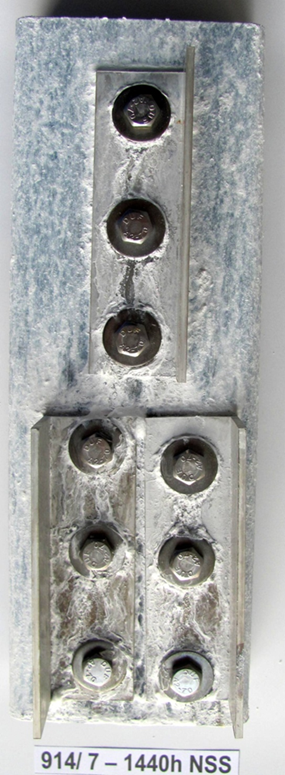
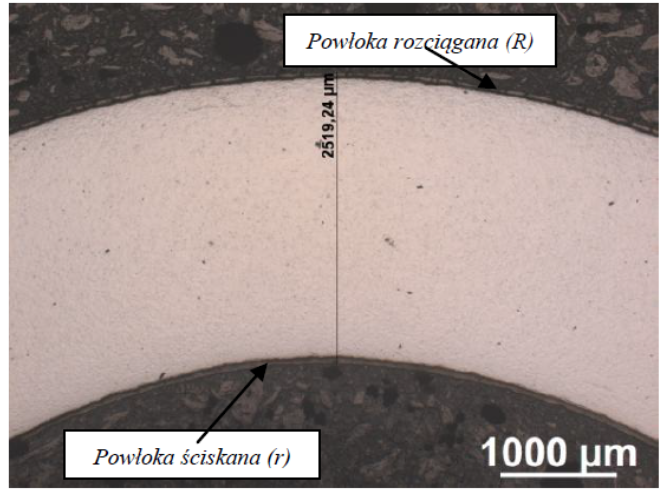
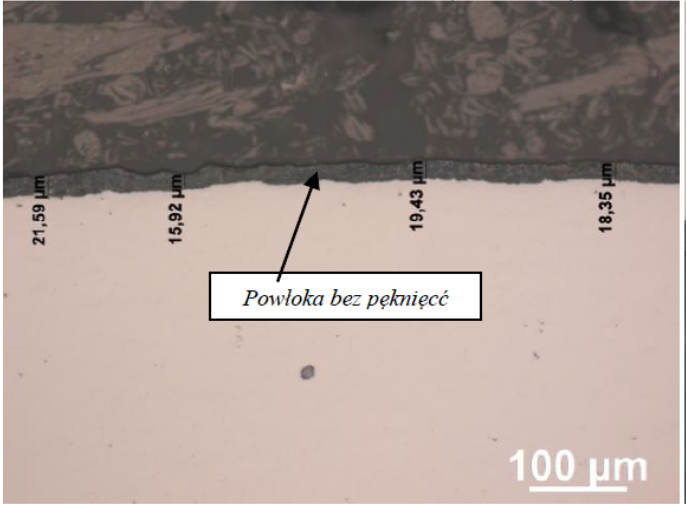
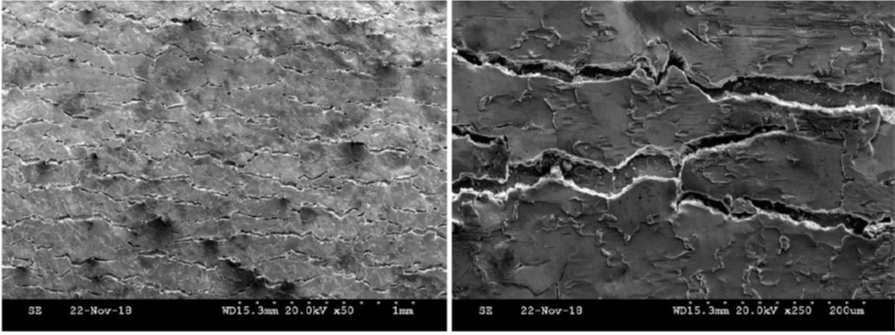